top of page
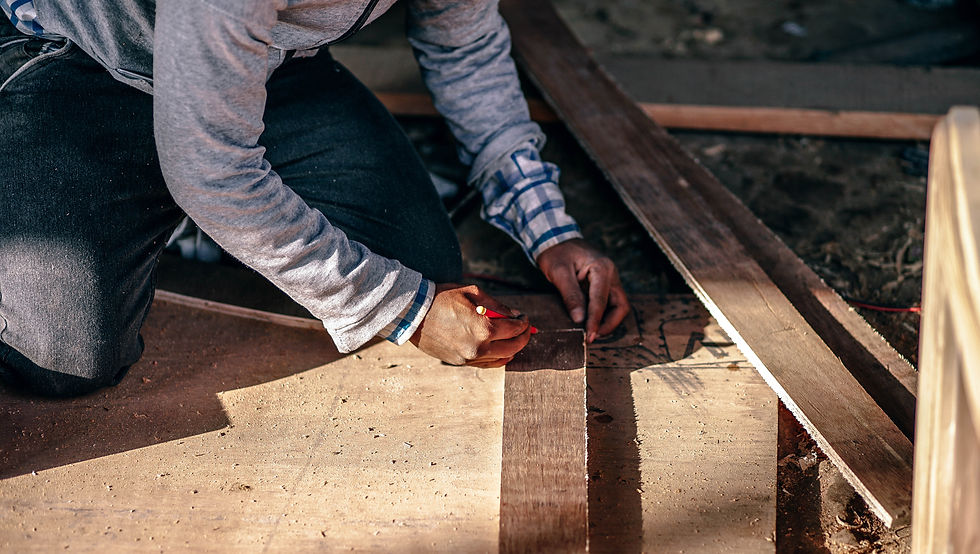
Service/Warranty Divison
Whether we built your building form the ground-up, renovated space or have not worked together before,
Wespac’s Service Division will make sure that your building looks and works as well as the day it was completed.
The Wespac Service Division provides ongoing property maintenance including residential repairs, small remodels and additions. A wide variety of both interior and exterior services are provided by our service professionals.
From lighting replacement to the weatherization of an entire building, Wespac has your day-to-day building needs covered to keep your building looking great and business running efficiently.
For more info, contact Ken Watson.
-
PRECONSTRUCTIONWespac’s team approach to every project gives you the greatest control over the quality, cost and schedule for your project. Our preconstruction services include coordination and all necessary input to assist the design process without compromising integrity. These services include items such as site-specific preparation, value engineering and procurement that go beyond the constructability and address overall project integration. At the end of the process, your project meets all functional, aesthetic and budgetary goals.
-
CONSTRUCTION PROCESSConstruction services remain identical for negotiated or competitive work. Safety, sound management, constant communication and complete quality control provide the focus for all of Wespac’s work. Using this full-service approach, we will expedite your project in record time and get operations up and running sooner. We can help streamline the complicated zoning/rezoning and permit processes and ease the transition during and after construction.
-
ESTIMATINGThe estimate is one of the most important tools used in every stage of the construction process. An accurate estimate, based on well-defined project criteria, is the key to maintaining project performance and long-term cost control.
-
VALUE ENGINEERINGValue engineering is an indispensable tool in all Design-Build projects. When implemented properly, the process can save client money, while preserving or improving project quality in ways that may otherwise be overlooked. Through multiple work sessions, the project team will determine the relative importance of each project design feature, material selection and system performance, and will develop a list of items to evaluate for possible cost savings. Experience has proven that subcontractor and supplier input contribute greatly to this process; therefore, subcontractors in key trades will be contacted and asked to provide suggestions. Additional work sessions allow for review and action on each item. The result is an integrated team approach which will include all parties to incorporate important considerations into the final project design.
-
SUB SELECTIONOver twenty years of building experience for some of the most reputable clients has provided many relationship-building opportunities with the most prestigious subcontractors. The pool of subcontractor relationships we have built over the past two decades provides the highest quality work that Wespac is known for.
-
PROJECT CONTROLSSelecting a general contractor for your project involves much more than a “low bid.” Every successful project demands constant communication, dedication, coordination and planning. Wespac Construction Inc. has developed a specific system of project management to capture all of these needs - Wespac’s Project Control System™. Wespac has a proven project management system that has been refined over more than 20 years to create a service that is unequaled in the construction industry. By implementing the Project Control System™ on every project, Wespac ensures client satisfaction; resulting in many repeat clients. The process begins with listening to gain a clear understanding of the client’s needs and continues with communication among the entire team to ensure that all parties maintain the desired goal. The end result is satisfaction and appreciation.
-
SCHEDULINGDuring the preconstruction process a master project schedule is created based on a Critical Path Method (CPM). This is used as a communication tool between all key stakeholders in the project, including the subcontractors to clearly define project milestone dates and schedule completion dates of trades.
bottom of page